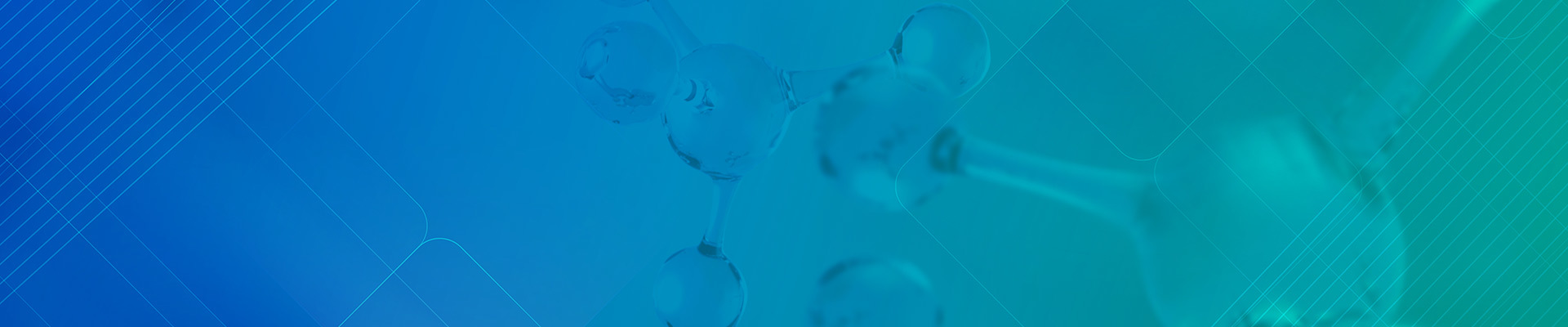

1230 H54-31-1 general pure epoxy coating
Category:
Keyword:
1230 H54-31-1 general pure epoxy coating
Details
Product introduction
1230 is a two-component modified phenolic amine-curedgeneral pure epoxy antirust coating.It has fast dryingperformance and can be normally painted and cured at lowtemperature. The paint film is tough, wear-resistant and hasexcellent corrosion resistance.
Recommended applications
For atmosphere and immersion conditions. As a general coating, itcan be used in ship bottoms, ballast tanks, anchor chain tanks, docksteel piles, offshore oil drilling platforms, hydraulic steel gates, minesteel supports, internal and external walls of pipelines, etc. forheavy-duty anticorrosion.
Product information
Appearance:Gray/aluminum red
Volume solids:72±2%
Proportion:3:1(volume ratio)or 5.14:1 (weight ratio)
Mixture's pot life:2h (20℃)
Full cure:7d
Recommended DFT:125 μm (corresponding WFT=174 μm)
Theoretical quantity required (125 μm):5.8 m²/L or 3.9 m²/kg
SG:1.5 kg/L (SGs are slightly different for different colors)
Flash point:Above 35℃
VOCs:258 g/L
Construction conditions
New steel: Sand blasting to Sa2.5 and Medium(G) surfaceroughness(ISO 8503-2).
Steel coated with shop primer: Cleaning for sand blasting orgrinding with an elastic grinding wheel to polish the corrodedparts to St3.
Use welding, flame cutting or hot work to correct the burnedparts:Remove the welding slags and spatters, grind and then polish it to St3 with an elastic grinding wheel.
The substrate must have a temperature >3°C above the dewpoint. The environment should be <85%RH.
Use this product only when the painting and curing can becarried out normally at above -10°c. The painting surface mustbe clean and dry.
Painting method
Painting methods:airless spraying/air spraying/brush coating/roller coating
Diluent:103 epoxy diluent
Dilution:0-5% of the coating weight, The actual addition may be adjusted according to the field painting method
Nozzle size:0.23-0.29 mm
Spraying pressure:15-20 Mpa
Drying time | ||||
Temperature | 0℃ | 10℃ | 20℃ | 30℃ |
Surface drying | 12h | 8h | 4h | 2h |
Hard drying | 24h | 12h | 6h | 3h |
Repainting interval | |||||
Subsequent coats | Temperature | 0℃ | 10℃ | 20℃ | 30℃ |
Epoxy | Shortest | 12h | 6h | 3h | 2h |
Longest | 90d | 45d | 21d | 14d | |
Polyurethane | Shortest | 12h | 6h | 3h | 2h |
Longest | 7d | 5d | 72h | 72h |
Film thickness:Non-recommended film thickness may be adopted according to the purpose and area. But this will change the coating rateand affect the drying time and repainting interval. The normal dry film thickness of a single coat is: 75-200ym. Ballast tank:Airless spray for 2-4 coats, with a DFT of 300-400um. 0ther parts: Airless spray for 2 coats, with a DFT of 200-300μm.
Packing specifications:Component A:13.5L,component B:4.5L or Component A:23.1kg,component B: 4.5kg
Shelf life:Base material: 36 months , Curing agent: 12 months
Safety measures:Refer to our Material Safety Data Sheet(MSDs)
Disclaimer: The above produtiformatin and data are accumulated acordina to ou experience in experiments and pracicaluse, and can be used as a constuction quideFor painting works that we are not informed, we ony guarantee the qualty ofthe coating itsel,butwe are not responsilble for other problems. We have the righto modify thimanualdue to the continuous improvement of our product.
Relevant products